Mechanical Solutions
Experieced Expert of Composite Material Chassis
Engineering Design Service
Engineering Design Service
The birth of a new product must undergo a series of processes from concept generation to product design, fabrication design, and mass production. In new product development, some firms will outsource a portion of its design and fabrication tasks, including model sampling, circuit design diagram, product prototype design, tooling, pilot runs, and terminal mass production operations. If there are multiple outsources, product developers must expend considerable amount of time communicating with vendors. When conflicts occur in electronic and parts designs, the exact problems cannot be correctly conveyed and solved, delaying product launch into the market.Getac is an internationally acclaimed manufacturer of electronics and mechanical parts and also one of the few companies equipped with the expertise in electrical, electronics, and mechanical part engineering. Our fab plants are well-equipped with talented technicians and advanced equipment to render services that can meet the diverse needs of customers, including circuit board design, power supply design, optical module bonding, mechanical part design and fabrication, and integrated electronics and part products.

- Concept product designs and technical solutions
- Product external design
- Product development and engineering design
- Hardware design and PBC layout
- Process development and mass production feasibility analysis
- Rapid prototype, pilot runs, and mass production planning
- Integrated electronic, mechanical, software, and automation solutions based on customer needs
- Process failure mode and effects analysis (P-FMEA) and project management
- Product Mass Production
Getac is committed to improving the quality of product and engineering designs, using the state-of-the-art computer software aided designs and validation process in hardware design, mechanical design, engineering design, testing and validation, and mass production analysis. Early corrections of deficiencies are made following simulations and analytical interpretations to provide reliable feasibility analyses, which reduce the cycle time and cost of product development for customers, thereby achieving effective cost control. Thus, maximum resource efficiency is achieved to enhance the effect of new product development.
We adopt advanced computer-assisted design and engineering systems, including:
- P-FMEA
- CAD three-dimensional modeling(Pro-E Creo2.0, Pro-E Creo 3.0, Solidworks)
- Finite element analysis(Ansys, Nastran)
- Electronic system heat-dissipation analysis(Flowtherm)
- Mold flow analysis
Specialist Teams in Electronics and Mechanics
Getac has accumulated years of experiences in the development and mass production of system products and mechanical solutions. The Company has a rich pool of experienced specialists in electronics and mechanical design, who can provide technical consults in both electronics and mechanics. Getac maintains close cooperation and active communication with its customers, subsequently elevating product design and quality as well as the feasibility of mass production to aid customers stay abreast of project progress and control their budgets for product development.
100% In House Mechanical Design and Production
Getac offers a one-stop total mechanical solutions, including product sampling, design and fabrication of mold prototypes, tooling, pilot runs, and production and assembly.
- Conceptual Design and Technologies Exploring
- Rapid prototyping and proof of concept (POC) units
- Batch type Pilot run samples (Engineering Builds)
- Soft tooling pilot run (Production Builds)
- Mass production and Assembly
Prototype & Pilot Run Service

Mock-up and prototypes can help product developers foresee and stay abreast of the effect of the finished product, staying well-prepared for subsequent commercial planning.Getac Product Modeling Center offers the most complete product sample manufacturing service, providing mock up samples and prototype designs for product development. The Center also conducts production assessment on ad hoc basis as well as pilot runs or mass production planning, during which it assists customers with complete product designs and production details that facilitate the successful commercialization of the product in the market.
To meet customers' diverse needs for material quality and external design, our plants are equipped with all types of processing equipment for advanced plastic and metal modeling, to afford complete range of model production and surface processing technologies, including computer-assisted engineering (CAE) technical support, CNC cutting sheet metal forging, molding, and assembly, silicon mold placing, soft mode, surface processing, and product assembly and delivery services.
- Plastic modeling equipment: CNC vertical machining center (VMC), vacuum casting, electrical discharge machining, screen printing, laser engraving, spray painting, and sand blaster.
- Metal modeling equipment: Laser cutting, numerical control press, bending, hydraulic press, welding, riveting, and drilling and tapping
- Assembly equipment: UV dispenser
Electronics development involves electronic and mechanical designing, subsequently entering mass production followed by a whole new profession involving fabrication and post-processing technologies. Getac is one of the few professional mechanical manufacturers specializing in electronics, mechanics, and process technologies all at the same time. It has accumulated years of experience in product development and product commercialization. Its R&D engineering team is able to provide customers the most professional opinions at the product development stage, while quickly and flexibly responding to customer needs, including simple parts, modules, to complex mechanical designs. Additionally, to prevent disclosure of customers' confidential information thereby incurring reputation loss, Getac team members are required to comply with the Company's regulatory requirements with regards to trade secrets and intellectual property rights.
Getac is an internationally affirmed mechanical solution provider, affording one-stop mechanical solutions, ranging from mold prototype, mold designing, tooling, plastic injection, to surface processing such as coating, printing, and assembly for delivery, all of which are performed in-house. If customers wish to incorporate the mold prototype in production, we can do so immediately as requested, thus shortening the process of transfer from mold prototyping to mass production.
Tooling service
Tooling Service


Complete precision processing and measuring equipment
- Precision processing equipment: CNC processing machine (n=23), electrical discharge machine (n=16), wire-cut machine (n=8), porous processing machine (n=2), high-gloss mirror processing machine (n=7), milling machine (n=24), radial drilling machine (n=2), deep-hold drilling machine (n=2), grinding mach
- Measuring equipment: 3D blue-ray scanner, coordinate measuring machine (CMM), computer microscope, computer altimeter, Rockwell hardness meter, hardness meter - G&R, surface roughness instrument, and various types of tool measuring instrument
To improve mold design quality, Getac adopts cutting-edge computer-aided engineering (CAE) technology to conduct an in-depth mold flow analysis on product structures before mold development. In addition to auto-CAD 2D design software and PRO-E software, the most advanced MODEX 3D simulation technology and NX (UG) 14 interactive CAD/CAM (computer-aided design and manufacturing) system are also employed to realize all types of molds of complex models and styles. Furthermore, before the tooling process, injection defects are predicted and mold designs are corrected following simulation and analytical interpretations to reduce the costs and time spent on testing the mold, which effectively shorten the product development cycle.The number of days in a cycle of plastic mold development at Getac differs according to the size of the mold and the design complexity. Generally, the development of small-to-medium product molds requires 14 to 25 days on average, and 30 to 45 days for large products. The actual number of days needed varies according to the complexity of a product structural design.

Highly Professional Service Quality
Getac has years of experience in designing and producing high-quality molds. Project management takes into consideration the mold design quality, production cycle time, cost control, and the feasibility of mass producing the final mold. Our project teams maintain close contact with our customers to stay informed of their needs, providing the most professional advises and solutions based on our previous mass production experiences. This is to facilitate product production at the mold-forming stage, thus eliminating the needs to revise external models or mechanical designs and helping customers reduce development costs and risks. Additionally, to effectively control project progress, Getac adopts specialized tooling management practices, including stringent control over design and processing progress and complete preservation of repair/maintenance records, to achieve optimal progress and smart scheduling applications.
Mass Production & Assembly Service
Getac mechanical Solution BG is a world-class mechanical part supplier providing years of services to internationally acclaimed customers, which include iconic customers and OEMs/ODMs across the world. Its product applications encompass consumer electronics, computers, communications, and cars. Getac is able to produce products in large quantities or in small quantities but high in diversity, providing comprehensive range of products and designs customized to customers' different needs through our efficient manufacturing abilities and customer services.
Service Scope
- Plastic-injected mechanical parts
- Composite mechanical parts
- Silicon rubber die-pressed mechanical parts
- Metal stamped mechanical parts
- Assembly of mechanical parts
The Best Multi-medium Heat&Cool Molding Provider in the Industry
Getac is the leading provider of the most mature Multi-medium Heat&Cool Molding(MHCM), which involves control over molding temperature to enhance the glossiness of plastic product surfaces, render seamless surface, and more perfectly present and replicate die surface patterns compared with conventional injection molding process. Regarding plastic products containing glass fibers, MHCM can reduce floating fiber surfaces and simultaneously enhance coating quality.

High-Tech Intensive Professional Manufacturer
Getac has a large pool of experienced and specialized R&D teams that continuously engage in the innovation and improvement of new materials, new processes, and surface processing technologies to produce mechanical products that are trendy, lightweight, eco-friendly, and durable. Regarding plastic molding technology, we continue to provide cutting-edge process technologies, using our mature MHCM technology as the basis:
- Double Injection Molding
- Insert Molding
- MuCell Injection
- Surface Processing
Metal mechanical parts: External processing such as anode processing, hairline finishing, sand blasting, etching, milling, and laser engraving
In addition to the aforementioned plastic casting technologies, metal stamping is also provided. Metal stamping is a production technology in which aluminum plate is placed inside the mold and subjected to pressure by using stamping equipment, thus casting into a mold. Aluminum alloy stamping can be combined with plastic injection materials to effective elevate structural strength of the product while reducing the subsequent assembly cost of the aluminum alloy product.
Years of Experience in the Mass Production of Composite Mechanical Parts
As the needs for trendy, refined, and lightweight products increase, consumers are provided with a brand new option of composite materials in addition to metal casing. Getac's MHCM technology is applied to composite materials, successfully improving the cycle time of product casting and the post-casting constriction problem. The resulting part features attractive appearance, higher rigidity, and more temperature resistant. Getac is the first manufacturer to introduce composite material casing, gaining considerable experiences in the project management and mass production of composite material casings. Getac mass produces the following composite materials:
- Amorphous plastic:Polycarbonate (PC), polystyrene (PS), acrylonitrile butadiene styrene (ABS), and (polyvinyl chloride(PVC)。
- Crystalline plastic: Polypropylene (PP), polyethylene (PE), polyamide (PA, commonly known as nylon), and polylactic acid (PLA)
Currently, Getac is the major supplier of ultrabook fiber-glass casing.ultrabookHigh-fiber glass casing is made using MHCM, MHCM which effectively removes floating fiber surfaces and renders seamless surfaces that that bright and trendy in appearance. Compared with expensive metal casings, high fiber-glass materials closely resemble metal in terms of weight, thickness, and rigidity. Fiber-glass materials are more affordable than metal, making them a perfect alternative to metal casing solutions.
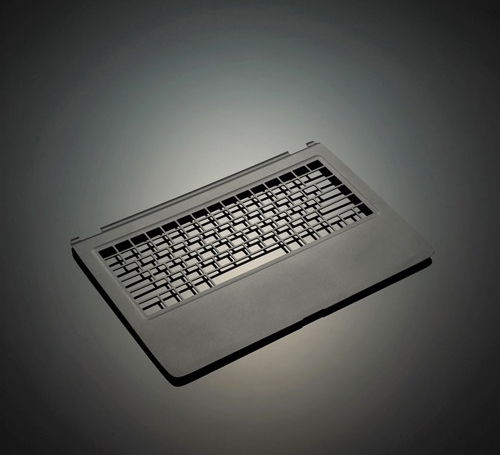
Pioneer of Composite Materials Chassis
The Pursuit of Aesthetics
We are blessed with a strongly capable R&D team that engages in the research and development of technologies and manufacturing processes to provide a variety of surface processing technologies for customers. Getac is also one of the leaders in new material development, attributed to its nationally certified laboratory that researches and develops novel composite materials to produce the most lightweight, ecofriendly, and aesthetic mechanical parts and create value for our customers.
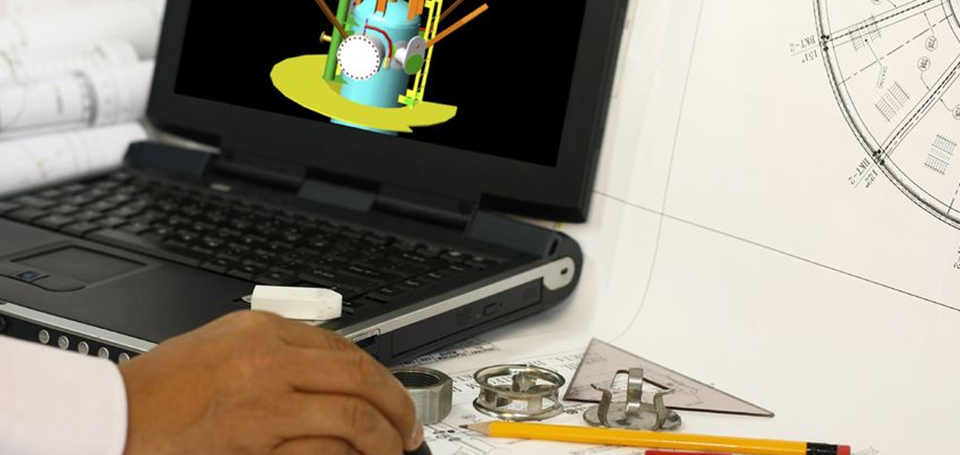
Comprehensive Mechanical Solutions
One-stop Shop Service
We offer comprehensive mechanical solutions, ranging from prototyping, mold designs, tooling, plastic injection, to surface processing such as coating, printing, and assembly. With our rapid, responsive, and all-in-one service model, we aim to meet customers' diverse needs and shorten the process of product commercialization.
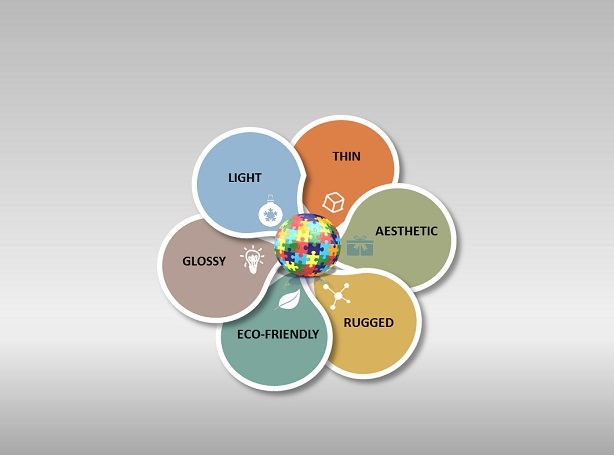
Leading Manufacturer of MHCM Process
Multi-medium Heat&Cool Molding Technology
Getac is the leading pioneer in Multi-medium Heat&Cool Molding (MHCM) technology, and we have gained numerous years of experience in project development. Compared with the conventional plastic injection technology, MHCM can enhance the glossiness of plastic product surfaces, render seamless surface, and more perfectly present and replicate die surface patterns. Regarding plastic products containing glass fibers, MHCM can reduce floating fiber surfaces and simultaneously enhance coating quality to produce trendy, aesthetic, and eco-friendly products